How Desperation Stimulates Short-term Rational Thinking…. and Long-term Demise
NOTE: This blog was written in the first two weeks of April, 2020. As such, it cannot and does not anticipate the full effect of the COVID-19 pandemic on the US and global auto industry. Stay tuned…..
In this series of eleven blogs, we will discuss the current situation in Detroit with the traditional “Big 3” – Ford, GM, and Fiat Chrysler (FCAU) – and their upstart rival Tesla. The series will end with specific recommendations as to what the Big 3 must do to survive against Tesla and other electric vehicle manufacturers. The eleven blogs in this series are:
- The Detroit Big 3’s current woes, Part 1
- The Detroit Big 3’s current woes, Part 2
- A brief history of the Big 3’s electric vehicle attempts, Part 1, GM
- A brief history of the Big 3’s electric vehicle attempts, Part 2, Ford
- A brief history of the Big 3’s electric vehicle attempts, Part 3, FCAU and General Big 3 Summary
- What’s so special about Tesla — Part 1, financials and battery performance
- What’s so special about Tesla – Part 2, manufacturing, and cost/time reduction
- What’s so special about Tesla – Part 3, coming Tesla models, etc.
- What’s so special about Tesla – Part 4, Tesla versus emerging competitors
- Why Tesla so successful……..the Company; the Cars
- What’s a poor Big 3 auto company to do now?
What’s so special about Tesla – Part 2, manufacturing, and cost/time reduction:
Manufacturing superiority and cost/time reduction:
As any start-up automobile manufacturer has experienced (or will experience, in the case of today’s startups such as Rivian and Byton), Tesla got off to a rocky manufacturing start, especially with the introduction of the Model 3 in 2017 and 2018. Their brand new company found that designing a new vehicle from scratch and getting it into volume production is no small task. Introducing more new and different vehicles in the same manufacturing facility only complicates matters further. Several years later, with hard won experience and Musk’s fierce determination and leadership, Tesla is now an absolute world leader in manufacturing expertise and automation. Furthermore, Tesla found religion about the importance of design for quality and manufacturability.
As an example of this, when performing a teardown of Tesla’s Model 3, Sandy Munro of Munro Associates found that there were some 70 or more different parts that were bonded, welded, or riveted together in the rear section of the Model 3’s unitized body/chassis. This poor design introduced great complexity, time, and cost into the Model 3’s production process. In Tesla’s just introduced Model Y, these 70 plus pieces have been replaced by two aluminum castings and one other part, for a total of three parts, achieving greater strength, lower cost, and a significant reduction in production complexity and time. Musk and his team are continually seeking ways to design cost and time out of their vehicles while providing even great value to their customers. One of Musk’s (many) favorite sayings is: “What matters is the pace of innovation”.
Equally important, another of Elon’s favorite sayings is: “The best part is no part.” No part means one doesn’t need an engineer to design it or a manufacturing engineer to design its production process, or a machine(s) to produce it, or a purchasing agent to buy it, a supplier to provide it, shipping or in-plant containers, stock in inventory, spare parts in inventory and so on. Note how much of Tesla’s total vehicles’ content consists of the same basic parts common (or software configurable!) across all vehicles – electric motors and drivetrains, battery management systems, vehicle management systems, Autopilot software, etc.
Manufacturing Plants: Since 2008, all Tesla products have come from its Fremont California plant, acquired from GM/Toyota’s NUMMI in 2010. In December Tesla’s new Giga Shanghai China plant opened, at this point dedicated to making Chinese versions of Tesla’s Model 3 for the Chinese market. At an estimated 2 million square feet (Phase 1 only!), the Giga Shanghai plant was built and operational in less than one year! This accomplishment was unheard of in the auto industry.
The Shanghai Giga factory gives Tesla multinational capability and relieved the Fremont plant of having to produce their high-volume Model 3 Teslas and ship them over the water to China, a process that consumed a lot of inventory for many days on the water and in loading/unloading and on customs docks. Furthermore, it eliminated the not insignificant damage to Tesla’s vehicles that resulted from loading and unloading and moving them around. It also relieved Fremont of the much added complexity of building a vehicle for the Chinese market – – with its different regulations and requirements, right down to the stickers (in Chinese, of course) routinely required in various places on each vehicle.
In early 2020, Tesla has started construction of its new Giga Berlin manufacturing plant about 30 miles outside Berlin, Germany. As with Giga Shanghai, this plant will also relieve Fremont from the high volume production requirements of Teslas made for Europe, and from the aforementioned overseas shipping and specification complications they entail.
By mid-2020, Tesla will likely announce their fourth Giga plant dedicated to Tesla’s Cybertruck and Model Y, production that will be located in the central or southeastern US. Current prospective sites are Austin, TX, Atlanta, GA, or Nashville, TN, with Austin clearly being Elon’s favorite given its hi-tech reputation, that it has an enormous pool of excellent software engineers, and because Texas leads the US in pickup truck sales. Each new Tesla Giga auto plant ramps up its production quickly to its so far demonstrated capacity of about 500,000 Tesla vehicles a year.
Tesla has a formula for quickly erecting standardized plant designs and equipping them with state-of-the-art production technology and automation. This is in part aided by Tesla’s 2017 acquisition of Grohmann Engineering, based in Prum, Germany, a superb German manufacturing engineering and automated production equipment company. Right on the heels of acquiring that company, Musk declared that Grohmann’s work for German auto companies would stop and that they would dedicate the company’s efforts solely to Tesla. This decree did not make the German manufacturers happy, especially Daimler Benz and BMW.
Two additional Tesla manufacturing plant questions remain at this point. The first is where will Tesla’s Semi trucks be built. These will initially be low volume production, despite Tesla’s over 2,000 order backlog for these vehicles. My estimate is that these will be built in Fremont or very nearby. Or, because the Semis will consume so many batteries, it may be less costly for Tesla to produce their Semis next to their Giga Reno, NV, battery plant.
As all Tesla aficionados know, Tesla’s vehicle production is currently constrained by Tesla’s (and currently, Panasonic’s) battery production capacity. Pouch-style batteries from CATL will be installed in most Model 3 production from Giga Shanghai from 2020 on. This will offer some relief on cylindrical-celled battery availability for the US and rest-of-world market.
On Tesla’s battery technology day scheduled for this month (April, 2020), Tesla is expected to make several major announcements about its improvements in battery technology and battery production process, and the resulting improvements in battery energy density and battery pack power, all affecting the range of Tesla models and the charging life cycles of their vehicle’s batteries. It is clear that Tesla is ending its agreement with Panasonic and intends to pursue its vertical integration strategy even further by producing its own batteries. Tesla’s battery day announcement will forecast whether Tesla can continue to rely solely on its Giga Nevada battery plant’s output or whether another dedicated battery plant will soon be needed. In my estimation, another two Tesla battery plants are essential, and they would likely be located adjacent to Tesla’s forthcoming Berlin and Cybertruck/Model Y facilities.
We can estimate Tesla’s annual production of vehicles with only the plants planned above. It might look like this, in thousands of vehicles, not counting Semi trucks:
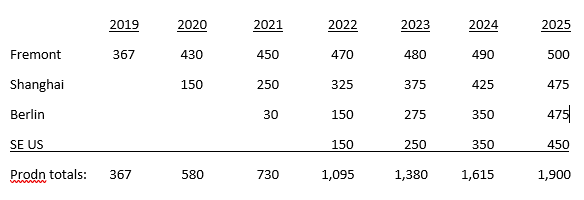
Just ballparking, 1,900,000 vehicles a year at $56,000 per vehicle (2019 average selling price across all Teslas = $56,632) would produce a car/pickup only revenue stream of $106.4 Billion in 2025, up from a total company revenue of $24.6 Billion in 2019! This represents a compound annual growth rate (CAGR) of about 26.5% for Tesla vehicle production.
Note: These estimates do not take into account Musk’s continual improvement credo embedded in Tesla’s culture and the resulting incremental production gains at each plant due to improvements in design, production technology, and production processes, in addition to the increasing knowledge and skill of Tesla’s workforce. You might estimate that the combined total of these improvements could add 4% improvement per incremental year to the annual rates shown above.
Blog #8 in this series is: What’s so special about Tesla – Part 3, coming Tesla models, etc.
Photo courtesy Pixabay
Your feedback in the form of comments or suggestions are welcome in the comment window. Thank you for following my blogs on this site and for participating in my blogging community.